Shoe Surgeon: Dominic Chambrone Chops Up Kicks!
Dominic Chambrone simply refuses to accept the status quo. With scalpel in hand, the self-proclaimed ‘Shoe Surgeon’ has made a name for himself by dissecting footwear to the core elements, unashamedly challenging the sanctity of brand identification. With a background in traditional shoemaking, Dominic has brought his old-fashioned skills to the custom world. The Los Angeles local is now set to make the transition from 1-of-1 customiser to fully-fledged shoemaker with the impending release of his very own scratch-built designs through the Rooy platform. We enter the operating theatre to find out what the master surgeon has in the works.
We heard you’ve been very busy lately.
Yeah, I basically had to move my entire workshop in two days. The move was actually really stressful because my finger almost got fucking cut off. Two of the workers dropped a machine on my hand and sliced the finger tip off. It went right through my nail bed, but luckily missed the bone. Half an inch was hanging right off.
Ouch! We hope the move was worth it at least.What’s the new workshop like?
Much bigger and it’s completely my own space. I was sharing a space at the old workshop, so it’s great to just have a place all to myself. It really helps to get good energy flowing without anyone to mess up the vibe.
Shoe Surgeon is obviously now a full-time thing?
Yeah. Shoe Surgeon’s more than full-time. I don’t fucking sleep. It’s the life of a creative slowly turning into a businessman. This was never supposed to be. I just wanted to make dope shit! I just wanted to create, and now the only way to keep creating is to get your business right.
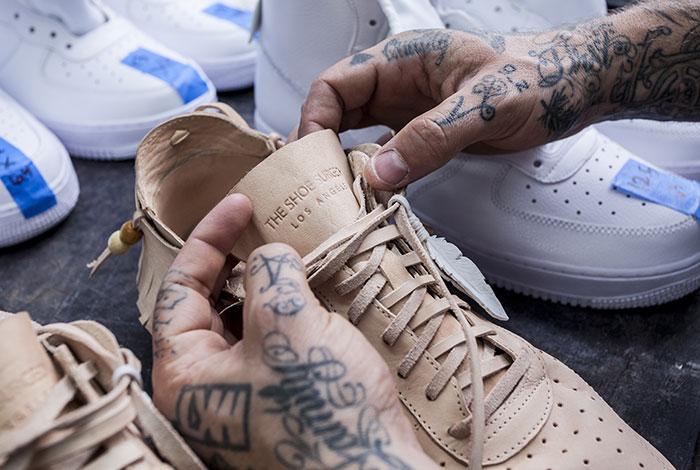
You ever see yourself working for a brand?
The only way I would ever do that is if it makes sense, but I would never be able to work solely for one company or person. I met with Nike already and basically they ‘own’ you. You can’t do anything, so that right there is a red flag for me, even if they paid me well. I guess the stress is worth it for me to be free and create. That’s just my whole life. I’ve never really had a full-time job. Ever since I was young, it was just me creating and trying to do this shoe thing, and everyone was like, ‘What the hell are you doing? You’re wasting your life.’ My friends were making $20 an hour out of high school and that was a lot of money, but I kept just messing with shoes. And finally, it’s all changed. So I would work for a company, but not where I get paid to give them all my ideas.
What was it that inspired you to get involved with sneaker customisation?
What got me started was back in high school when I stumbled upon Jordans. My cousin was 10 years older than me, and she let me wear her original 1985 Jordan 1s. I was a freshman and all the seniors had other Jays, but when they saw those they just went nuts. Later on I started working at a sports store. We had Jordans before they were even released and people would freak out. Then, soon enough, everyone had the same fucking shoes, and I got sick of that really soon.One day, I picked up an airbrush. At first I bought model paint – definitely not the right stuff – but I took these all-white Air Force Mids and airbrushed them in camo, and they turned out fucking amazing. I wore ‘em the next day and everyone just went nuts. Once I got better paint, things kept progressing, mostly self-taught. A lot of fucking up, a lot of money wasted. Well, not really wasted, it was all learning.
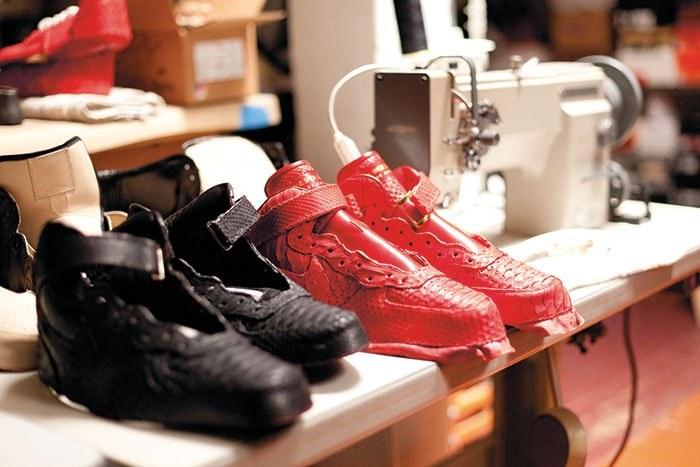
Did you get any formal training after that?
I hit up a couple of shoe repair shops but had the door pretty much slammed in my face. It’s definitely not an easy industry to get into. Eventually I went to this one repairer and he was nice enough, but when I asked if I could learn from him he turned me down, because I’d be a liability. So that got my hopes down, but the next day I went back into the shop anyway and told him I wanted to watch. We had an account doing Red Wing boots where we’d resole them, do heels, repairs and rip work. I soon started experimenting by putting Vibram soles on Vans and then I began doing the whole sneaker-boot conversion. A year later, every company was doing it. It was cool to do a custom or two, but when big brands were trying to produce them, they weren’t really selling, because no one really wanted a sneaker boot. They’d rather have a sneaker or a boot, but not both in the one shoe.
You’ve made a real name for yourself in LA as the go-to-guy for celebrity customs. Which famous names have Shoe Surgeon originals in their crib?
Trinidad James has a couple of my pairs now. We’re actually working on a few projects together at the moment. He’s a pretty big sneakerhead. I also just finished up a pair of buffalo Air Jordan 1 high-tops for Young Thug.
Nice. You made a quite a few shoes for Justin Bieber back in the day didn’t you?
I used to do all of his tour shoes. Now that I’m back in LA, I can do all of his more upscale shit. Before it was just kind of like teeny-bopper stuff. When you’re on tour, it’s flashy rhinestones, studs, all that bullshit, which I never really liked doing. It’s just something I had to do.
Did it help business?
Making shoes for him was cool, but it never really helped my business monetarily because most of his fans are little girls and boys that didn’t understand how a custom shoe should cost more than a pair of Supra. I never made any sales based on that relationship.
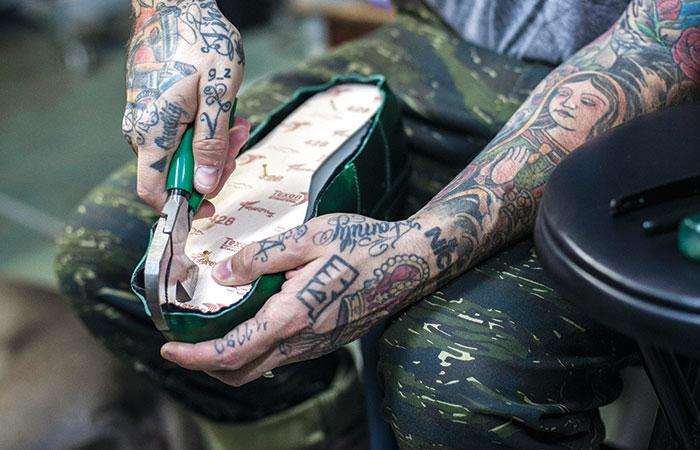
What has the deconstruction of sneakers taught you about modern manufacturing techniques?
Basically, how every brand is trying to do everything cheap. You can see the corners they cut and the new methods with which shoes are being manufactured so they can save money and time. It’s faster. Being in shoe repair for five years, I was able to see how to fix shoes. By taking shoes apart, I also got to see how older types of shoes were put together.
We noticed you’ve developed a taste for merging old and new lately. That Flyknit x Air Force 1 is on point and that Superstar x Boost fusion is crazy. Why retrofit these high tech lightweight uppers to such primitive bases?
I just wanted to do something different. When Nike came out with the Flyknit stuff years ago, I was fascinated by it. Basically I took the Flyknit Racer and then re-lasted it, so it has the shape of an Air Force 1. It’s not necessarily for comfort, because everyone gets upset that I put it back in a rubber sole, but it’s more just to practice my craft. A lot of the stuff that I do now is either accidental, because I have so many random shoes here, or it just stumbles upon itself. I have shoes and soles everywhere. I look to my left, I see a shoe, then I look to my right and I see a different sole. It just clicks. I put them together, take a photo and there it is.
Have you ever considered doing the reverse and fitting an Air Force 1 upper to the Flyknit sole?
I have, but you would have to rebuild the whole entire upper or you’re gonna see flaws from the glueing.
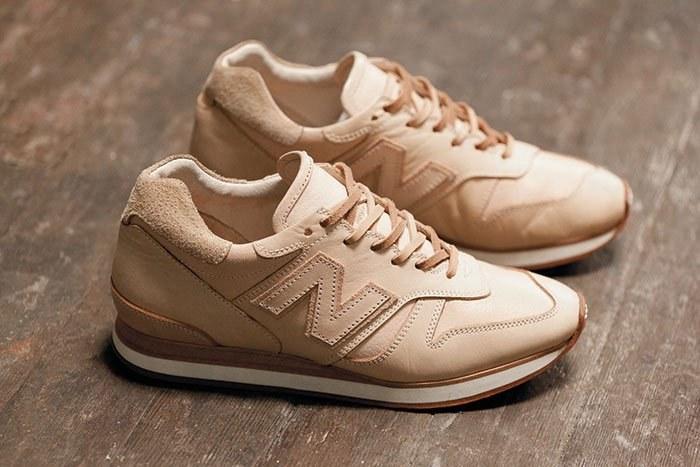
On the other end of the spectrum, you’ve got stuff like Hender Scheme which utilises traditional shoemaking techniques. Your addition of the New Balance ‘N’ to Hender’s MIP-08 was hilarious.
I’m addicted to collecting nice leathers and threads. Sometimes I spend all my money on that stuff and it piles up. Then finally when the time is right, I pull it out. I’ve been collecting veg-tanned leather for years, so it wasn’t that hard for me to find the right material, but it was really fun and something I’d wanted to do for a while. Not as a ‘fuck you!’ to Hender Scheme, but basically, to show everyone that buys Hender Scheme, that don’t really know why they buy it, that it’s just missing the logo.
We can’t imagine Hender Scheme were too happy with all the attention they were receiving over that one. Have you ever copped any grief from brands over your work?
New Balance loves me. [Laughs]. I’ve made friends with them, so I think they liked it. Some brands don’t really like their stuff messed with, but others don’t mind because it’s just extra publicity, I guess. It’s marketing.
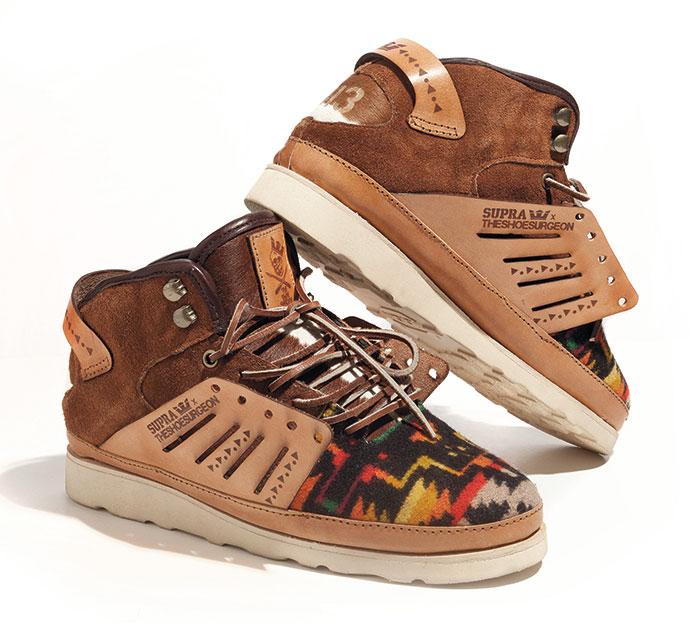
We heard you had some issues with Pendleton.
I was close friends with Supra at that time, and they sent me one of the Skytop IIIs early, so I customised it with Pendleton fabric and put a boot sole on it. I basically killed it. It is one of my favourite customs I’ve done and it got a good amount of press, back before customs were really big. I got a cease and desist from Pendleton, basically saying, ‘If this goes into production, we’ll sue you.’ I found out they were doing loads of stuff with Vans and Nike. They didn’t understand that I was just doing one-off customs
from a garage at the time. It was strange. I was scared at first, because it was the first big thing that happened, but I was like, ‘Whatever’, I mean, I bought the fabric and then made a custom shoe with my money. It’s not like I was doing production. I think they were just scared that it would basically take away from the Vans and Nike deals that they were working on.
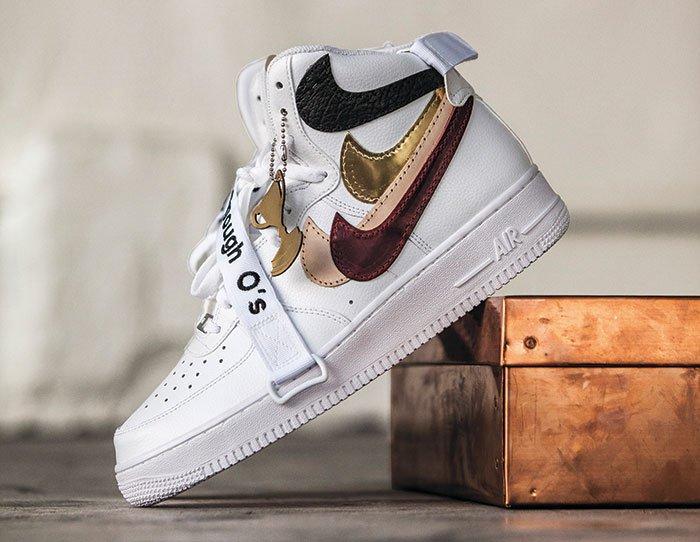
What did Nike say about ‘Misplaced Checks’?
They haven’t really said too much about it. I ran into a couple of guys from Jordan Brand at a trade show in Vegas, and they didn’t really say much about it. They just said that they follow me. It’s kind of a weird subject. Nike can do whatever they want but I don’t think they would do anything because it would look bad on them, going after a kid that basically started by buying Nikes, and now he’s doing his own thing. We pay full price and then we basically customise them, and John Gieger sells them.
So where does John come into the picture? He’s a designer isn’t he?
I would say he’s a ‘creative’. I guess the new term is ‘designer’, but that’s a very fine line, especially for CAD-spec designers. There’s a difference between customs, creative ideas and actual design. But I think that we’re all striving to become designers.
How did the concept come about?
I reached out to John after I dipped some Jordan 4s for him. He’s definitely a guy that respects art, and respects changing the normal. He had three ideas. One of them was to put Gucci fabric on a ‘Wheat’ Air Force 1. I did that and it looked really clean, it was cool. The next was Misplaced Checks. He sent me this crude sketch with all these Swooshes. Luckily, I’d collected a lot of leathers. I think we went back and forth with text messages and photos over 20 times. He posted them up and people loved it. Personally, I think they came out very nice. Once we did his first sample pair, there were some things he tweaked. He wanted everything to look symmetrical, because on the original, we had the Swoosh upside-down on some of them. A blog actually hit him up and they were like, ‘Yo, you should sell those because the response was insane!’ I never wanted to be doing so many custom Nikes in my life, but you can’t turn down money that is going to help you perfect your craft and move you forward. I think we made 25 pairs in that first run and sold them, it was insane.
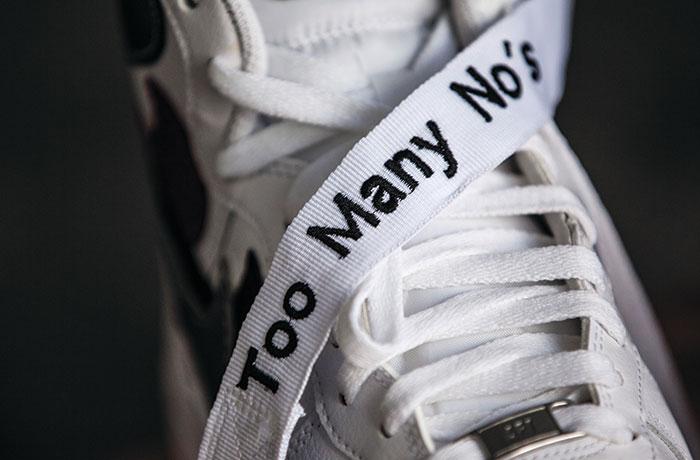
The quote printed over the straps, ‘Too Many No’s, Not Enough 0’s’. What’s the meaning there?
That was John’s idea. He had a relationship with Nike and I guess he brought a lot of ideas that I’ve been doing to them and they just shut him down, because he’s a nobody – he’s not Kanye West! ‘Too Many No’s, Not Enough 0’s’ means ‘Too many people to say no, not enough money!’
It all makes sense now. Is it true that you guys just love the trophy emoji?
Yeah, John loves that emoji, he has been using that trophy symbol since I began working with him, so it’s become a signature thing. He was using it on Instagram, so I drew it out and lasered out a bunch of trophies. That’s how it happened.
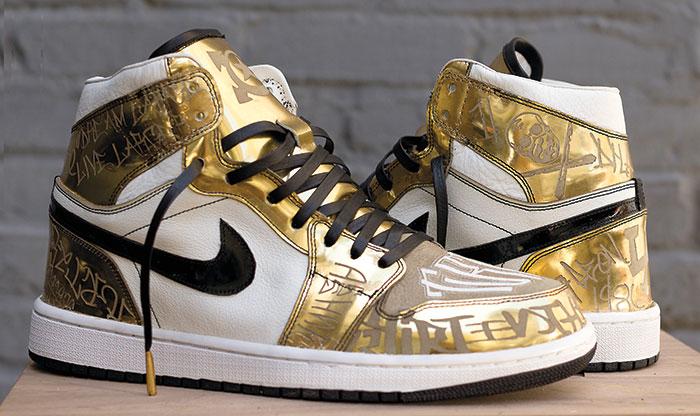
Nice touch. Speaking of metallic leather, you used that amazing gold stuff on the Entourage Air Jordan 1s.
My friends over at Shoe Palace were throwing an Entourage party and they came to me with this idea to make shoes for Turtle. I was thinking of making something from scratch, but then I figured it would be right if I basically mimicked the Entourage Air Force 1 but did it on a Jordan 1, because in the movie, Turtle now has money and only wears Jordans. They took a fucking crazy amount of work and they literally cost me $1300 just for the lasering, materials and the box. The leather is called ‘liquid gold’, it’s a metallic gold patent leather. When it came to the lasering, I went back and recreated some of the graffiti on the original, but then also made my own. I put Charlotte in there, which is where I actually got my first Sneaker Freaker magazine (Issue 3). It had a few pages on Mark Smith’s laser pack for Nike and ever since I read that I was fascinated by the use of lasers. I actually owned my own laser for a few years.
Crazy. How do you find working with lasers?
It’s just another tool to me, but once I bought my own laser machine, I found myself trying to run a laser business – and a shoe business. I was biting off more than I could chew. But using the laser as a tool itself is amazing. I’ll probably buy another one someday. Good ones are $30k, minimum. Cheap lasers cost a couple thousand, but I don’t like to buy cheap things.
So what did Jerry Ferrara think? Was he a fan?
Yeah, I think he liked them, but it’s not something he would wear, which bummed me out.
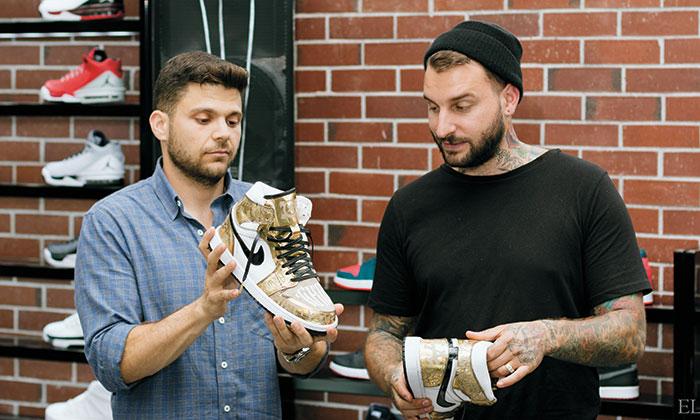
You turned heads when you posted a Frankenstein fusion of the Yeezy 750 Boost and Nike’s Air Yeezy II on your Instagram. What inspired you to create those?
There was no real inspiration behind it. I just had a Yeezy Boost upper and the Yeezy 2 soles lying around, so I thought it would be interesting to see how it actually looks together. A lot of kids out there are making all these computer-generated images but they don’t have the ability to actually make it for real.
I love seeing kids upset by that kind of thing. What’s the most difficult material you’ve worked with?
I have a friend who has a loom and she can hand weave fabric. She sent me a bunch of fabric, but you can’t cut it because it’s woven. It basically falls apart. There’s so much that goes into it. Basically, I have to iron it back on, and then I have to sew it closed, then I have to fold it. It’s a total pain in the ass. I’m looking into the actual bigger machinery that does wovens in sections. Knit is something I’m not very familiar with. I’ve been working with leather for over 12 years now, but knit is something I’ve always loved. I definitely think that the Nike knit shoes are made very well. That’s why they’re the price they are.
What would have to be the strangest custom you’ve done? Have you had any wack requests that you just had to turn down?
Yeah. Actually, a fairly recent one, this guy had a pair of Balenciaga Arenas and I put an Air Force 1 sole on them. I think it looked terrible. I don’t even know why I posted it, but some of the stuff we do is just to make the customer happy. You can be the artist and be like, ‘No, I’m not gonna do that,’ but sometimes you gotta please the customer. But even after those were done, the customer was actually like, ‘Oh yeah, those don’t look that good.’
I guess the customer isn’t always right, but the customiser is! What shoe do you want to tackle next?
Well I’m working on a few designs from scratch myself. I can build prototypes and create a pair of shoes from the ground up. I’m working on my own line of boots. When I got into shoe repair, I fell in love with Red Wings, Danners and Thorogood. I don’t just like Nike and adidas. I like everything. Honestly, I wanna get away from just customising shoes and build my own. Customising pays the bills, but it’s not where my heart’s really at. It’s not what inspires me.
Sounds like you need to start your own brand.
The Shoe Surgeon brand will always be customising, but I also want to be able to do other things, like start a school and teach kids. A lot of high school kids, they just don’t have anything. If they don’t play sports, then they’re usually lost. If we can get some of them into actually using their hands and making things, it could help them and the economy in the long run. I know it’s a long shot, but it’s worth trying. For a while, I was thinking about opening my own factory in the United States, where the younger generation would be able to work. To be honest, I lost faith in that concept. America fucked up, outsourcing everything to China. Basically, we have lost generations of people who make shit. Young American kids, they dream big, but they don’t wanna work hard for it. It’s pretty sad.
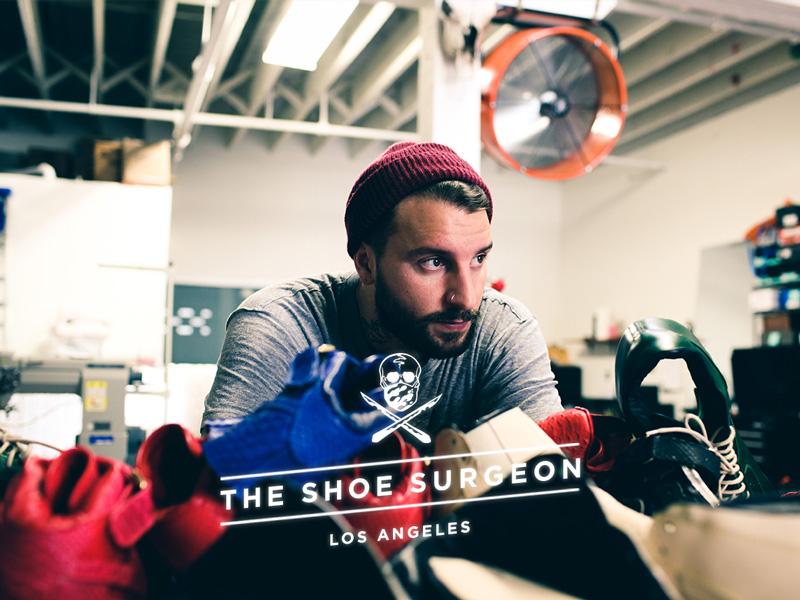
What is Rooy, sounds interesting. Is it a brand?
It’s basically a business platform that lets you design and produce sneakers. They have access to top-notch factories used by some of the biggest footwear brands and approached me with the opportunity to create my own shoe from scratch. They have faith in me to design and create something new, and that hasn’t really been done before. The whole time I’m fixing and customising shoes I’m always designing in my head. It’s the first project of its kind and it’s an open trade. You don’t really find too many customisers designing shoes from scratch or even starting their own shoe company, but the world is changing so quickly, it’s the way everything seems to be going. It’s exciting.
Who else are you working with?
I’m working alongside two other customisers, El Cappy and Sekure D. Our styles are completely different, so it’s gonna be fun. We’re actually going to the factory to see our stuff being made and choose the fabrics and materials. Being the first to do something like this is really appealing. But the best part is that I’ll actually be able to build my prototype and have it made exactly the way I want. It’s basically traditional shoemaking, but it works with sneakers just the same. If you create from nothing, instead of re-creating something... I guess you could say it’s a lot more satisfying that way. That’s what I love about Rooy! I feel like I’m finally evolving into the artist that I was really supposed to be.
What can we expect your shoe to look like?
I don’t know exactly, I have so many ideas and sketches already. My creativity is all spur of the moment, it just comes out naturally. The main thing is that I don’t want to just design a shoe that’s already on the market, I want to do something totally new. But in the end, it all boils down to making something that is gonna sell and still looks really good on the shelf, but stays true to me as an artist. That’s the challenge. I can’t wait to see what it looks like.