Material Matters: Nike HyperAdapt
The Nike Hyperadapt lacing system is one of the biggest innovations in sneaker-tech this year. The idea for an automatic adaptive lacing system was born in 1988 and has been an ongoing project at Nike’s Beaverton HQ ever since. Now that the official release date is just around the corner we thought it was time to focus the Material Matters lens back to the future of footwear.
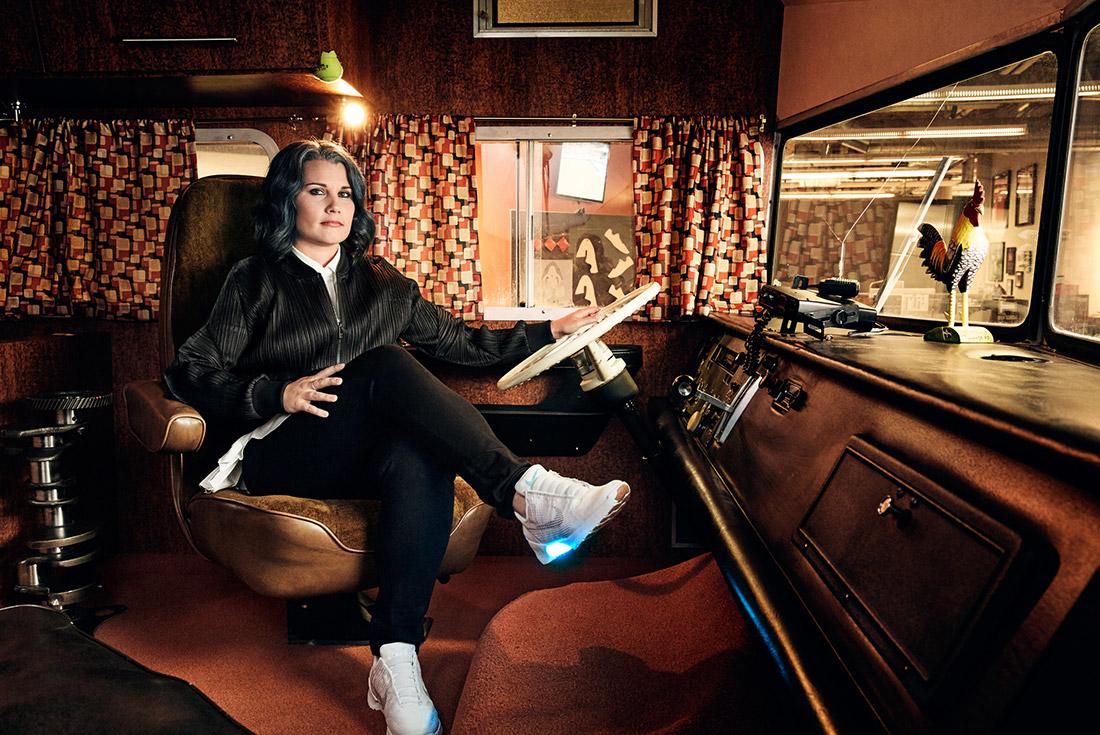
Tiffany Beers at Nike HQ, 2016. Pic via Wired Magazine.
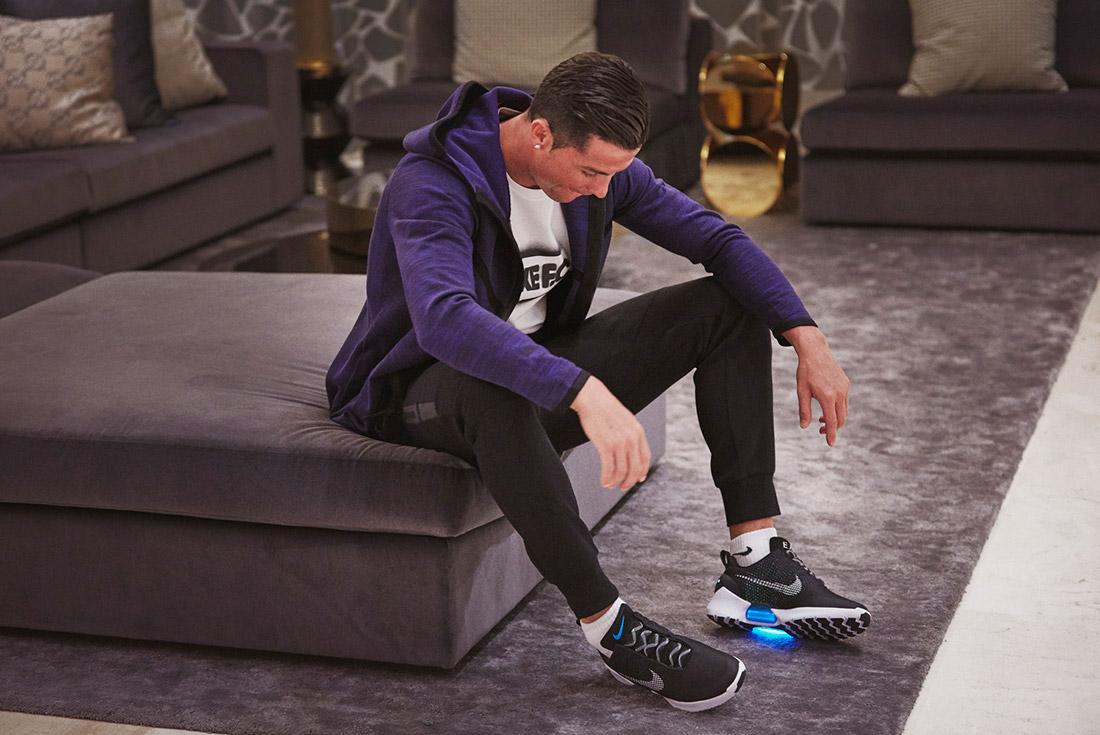
Cristiano Ronaldo tries out the Hyperadapt.