Material Matters: Nike Flyknit
Sneaker brands love to introduce us to the latest advancements in the footwear world. If you compare some of the shoes out there these days you’ll notice the big brands are engaged in a technological arms race in a quest for sneaker world domination. In recognition of the pioneering spirit we’ve decided to break down some of these features, week by week, in our new Material Matters series. Each edition will talk about some teched out aspect of the sneaker game, new and old, to help build a bigger picture of what goes on behind the mesh curtain of the industry.
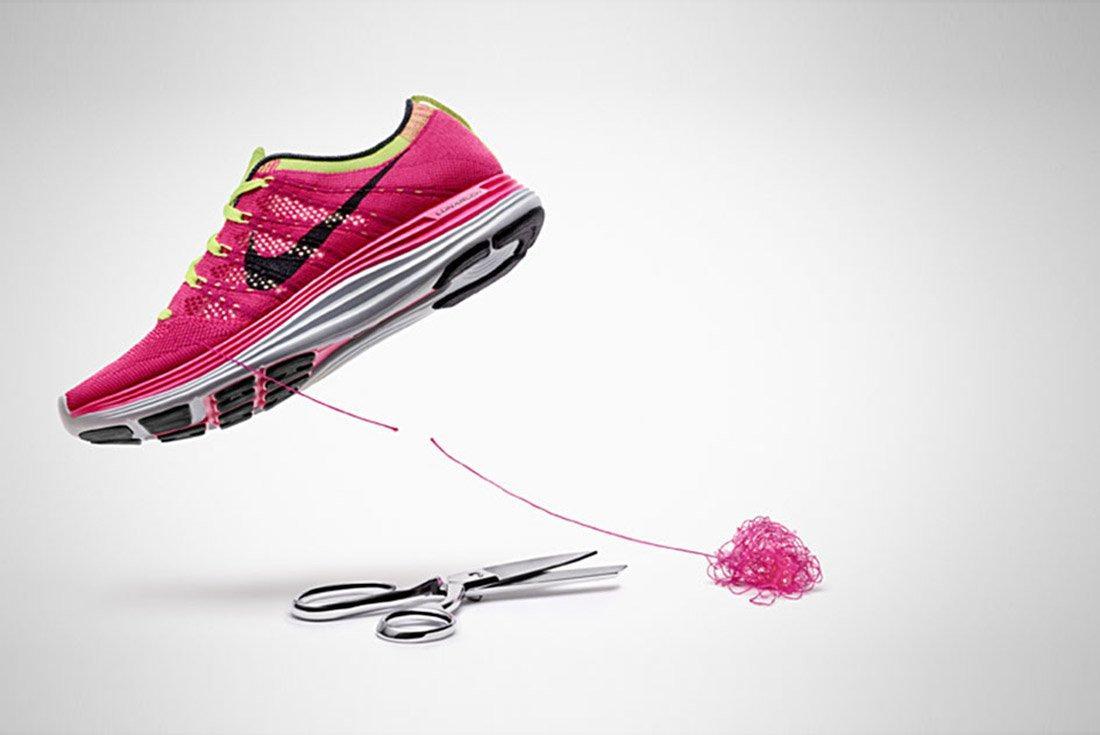
In recent Material Matters we’ve looked at Nike Shox, Cotton Canvas and adidas Boost Technology.