Reinventing Cool: Inside the adidas Climacool
has been keeping sweaty feet in check since the Y2K days.
First launched in the early 2000s, Climacool was answer to heat and humidity – a sneaker series that made airflow its mission, with bold designs built to breathe. Fast forward to today, and that legacy of cool hits .
This latest Climacool doesn’t just update the formula – it blows it wide open. adidas have ditched stitching, glue, and even traditional construction methods to deliver an industry-first: that offers 360° ventilation, featherweight comfort, and sci-fi vibes in spades.
We went behind the design with adidas to unpack how this boundary-breaking sneaker came together – from mood boards packed with wild architectural inspirations, to material experiments and tech breakthroughs that could change the way sneakers are made.
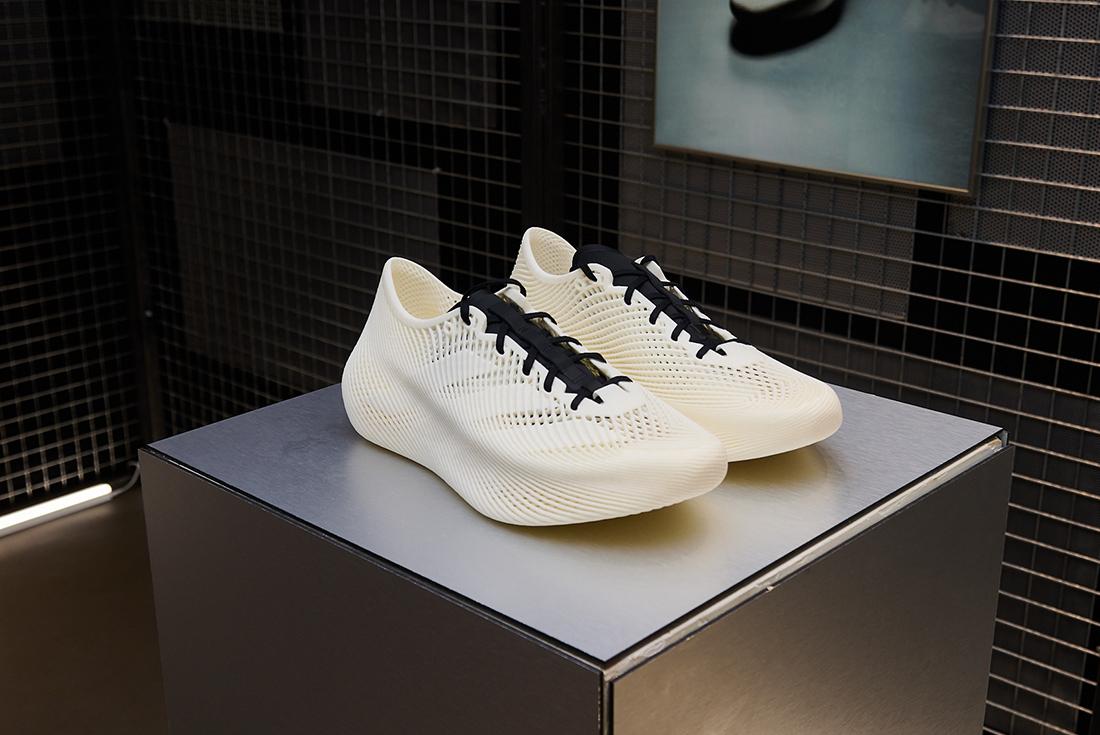
Let’s start from the top – how did the Climacool project come together, and what were the initial goals when it came to reinventing the line?
Climacool has always been about comfort, breathability, and innovation – this latest chapter takes that to a whole new level. We set out to create something that adapts to the foot in motion while pushing the boundaries of how footwear is made. The result is a seamlessly designed, fully 3D-printed shoe with 360° airflow, inspired by lattice structures in architecture that adapt to their environment.
What’s the most obscure material or tech reference that ended up on the mood board? Did any of those left-field ideas spark wild prototypes or ‘tech-speriments’ during the early concept phase?
We threw out the rulebook and looked at adaptive structures and materials that could change shape and support in real time. The mood board included references from nature and architecture, with a big focus on how form could follow function. That mindset led to breakthroughs in creating a new 3D printing process, and shaping a shoe that offers both support and airflow in motion.
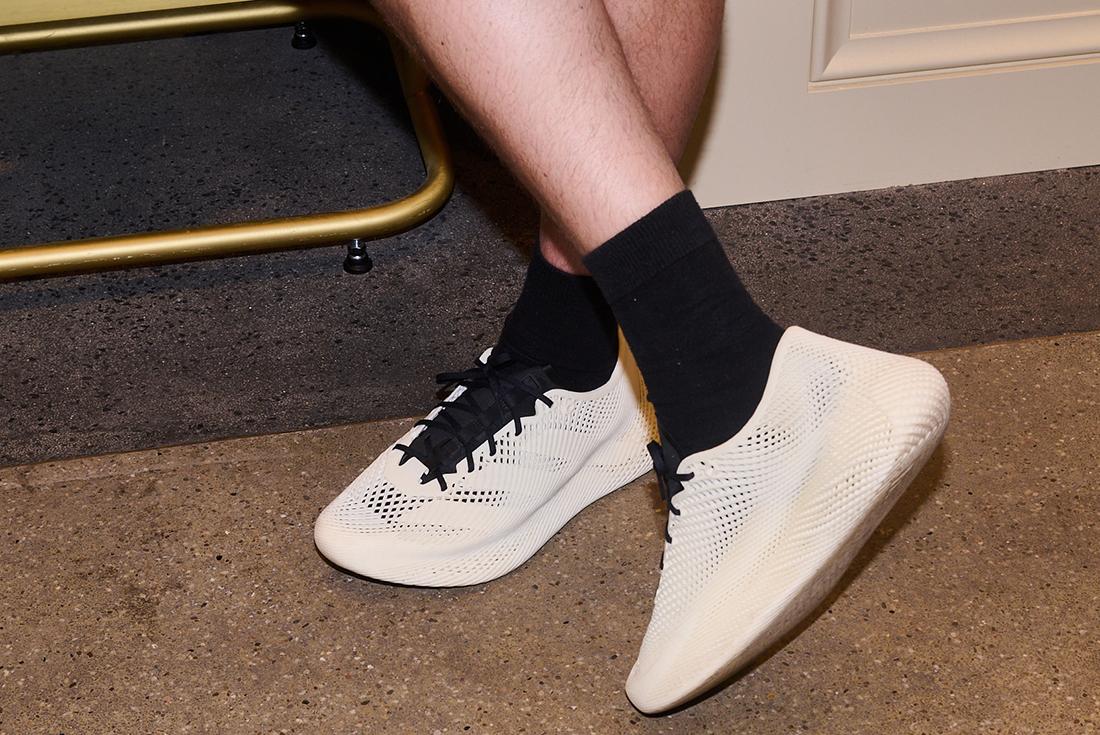
The Climacool boasts a fully 3D-printed, one-piece upper. What were the main challenges in achieving that seamless design?
We’ve 3D-printed midsoles for years, but printing an entire shoe was a massive leap. The biggest challenge was blending the upper and midsole into one seamless form using a single material. This meant rethinking traditional processes – no separate lasts for men and women, no stitching, no glue. It allowed us to integrate fit features like heel pillows and arch support directly into the design, for a more adaptive, universal fit.
The off-white colourway gives the shoe a clean, futuristic vibe. Was there a specific inspiration behind that palette and finish?
We wanted the form and printing process to shine. The off-white palette highlights the intricate structure of the shoe and the matte finish gives it a modern, refined look – moving beyond the glossy finishes typical of 3D printing. It’s a clean base that sets the stage for future colour explorations.
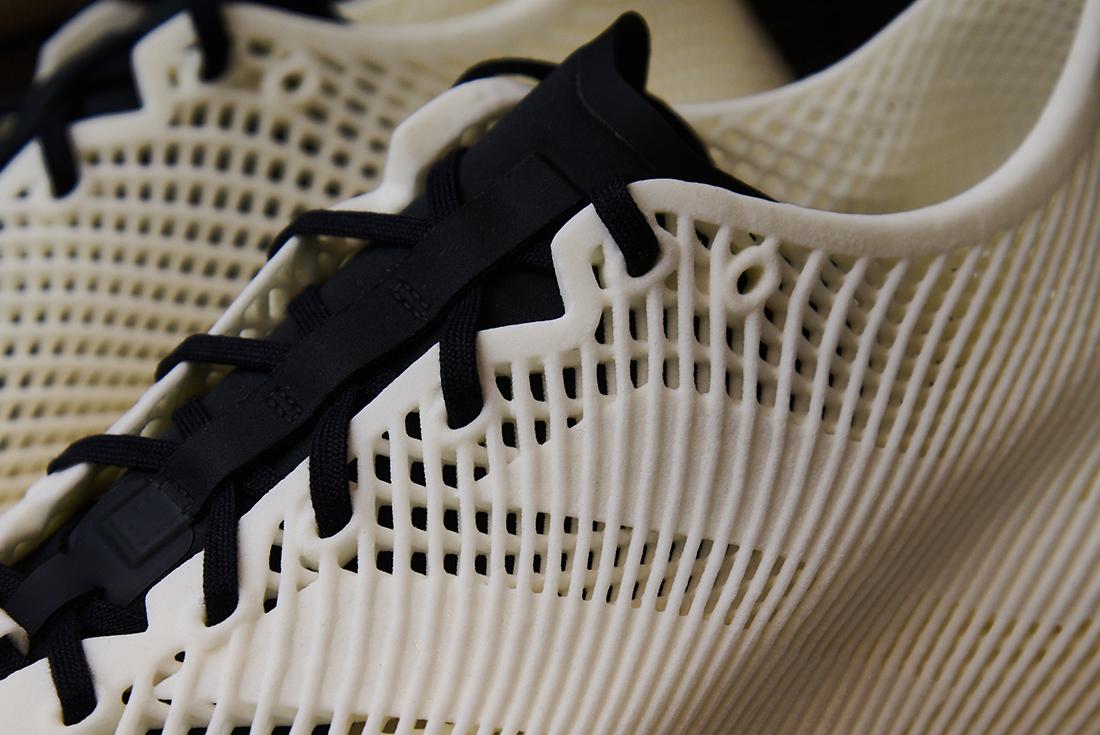
From a design language perspective, what makes a Climacool a Climacool? What were the must-keep DNA elements you couldn’t mess with?
Climacool is about delivering next-level breathability, comfort, and innovation. With this new approach, we’ve reimagined those core elements – creating a shoe that feels light, soft, and cool from every angle. The lattice structure and 360° airflow embody what Climacool has always stood for, but through an entirely new manufacturing lens.
How does 3D printing change the game in terms of the Climacool's performance and the on-foot experience?
Blending the upper and midsole in a single material gives a fit and feel that traditional construction can’t match. The lattice design flexes and moves with the foot, while maximising airflow for all-day comfort. It’s about revolutionary simplicity – even the ghost stripes on the sides strip things back to the essentials.
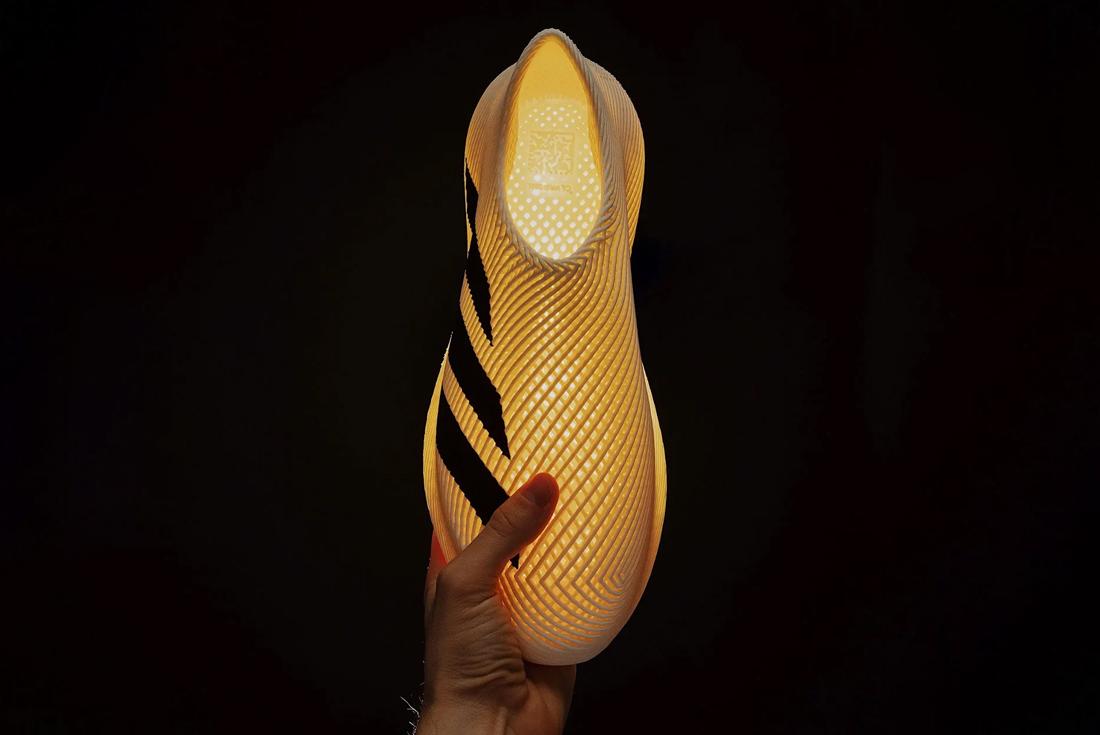
How did the development of this shoe process align with adidas’ sustainability goals – are we talking reduced material waste and/or a lower-impact production model?
Creating the shoe from a single UV-cured polymer drastically reduces material waste, and simplifies production. Fewer materials, fewer steps, less labour – it’s a cleaner way to make shoes. And this method opens up new possibilities for further reducing impact as we refine the process.
Do you see the 3D-printing techniques used here expanding across the adidas ecosystem? Could this be the start of a bigger shift in how the brand approaches sneaker construction?
Absolutely. Climacool is just the first step in a new era of footwear creation. We see huge potential in additive manufacturing to transform the way we design, fit, and make shoes – creating lighter, softer, more tailored experiences for athletes and everyday wearers alike.
What’s next on the Climacool journey?
This is just the beginning. We’ll keep evolving the Climacool experience, exploring new looks, feels, and fits, and expanding the lineup with both laced and laceless designs. Stay tuned – the future of footwear starts here.
The adidas will arrive on July 15 at adidas and select retailers. As always, keep it locked to Sneaker Freaker for updates.